- The geared extruder based on Wade's design
- Full electronics set for the machine
- Copper bar and cartridge heater for the barrel
So here's a few photos:
First, the extruder. This is how I assembled it, I believe this to be correct based on the illustrations I've seen

Here's another shot of the underside with the thermal barrier and nozzle installed

Here's the electronics along with the copper bar and cartridge heater

And here's a closeup of the cartridge heater
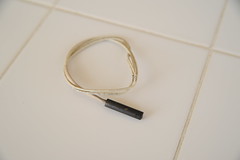
Onto the technical stuff. When I got the extruder in, it was pretty much perfect aside from a couple slightly little imperfections which were easily cleaned up. I used a squared file to rasp out the inside of the thermal barrier mounting hole and the PTFE barrier fits in fully and snugly. Just need to modify it a little for the mounting screws and I should be all set. It has a very tight grip on the filament and I was not able to budge it no matter how hard I tried.
The electronics came in, they were quite nice. There were a few touchups I had to do on the boards.. being all SMT they were bound to have a couple little problems, and they did, namely not enough solder in a couple places and a chip cap tilted up off it's pad on one side. Otherwise they seem pretty solidly built. I'm anxious to get them up and running with the steppers.
Finally, I got the copper bar and cartridge heater in from McMaster Carr. The cartridge heater seems perfect for the job, and the copper bar seems to have all the right dimensions for cutting it to fit. I'm going to attempt to build the heat transfer assembly I sketched out earlier, and I'll begin on that next week. The heating through the threads seems to be the preferred way of doing it, so I'm going forward with this.
Currently I don't have a lot more work done on it due to being away this week, however, next week I may have some time with a MakerBot, so we may be able to get some parts turned out to get it going. I'll keep posting pictures as I get more things and set them up.
I'm using a standard Makerbot Plastruder on my unit, but it shares the same brass barrel and PTFE thermal barrier as yours. On mine, the PTFE barrel is held in place by a retaining washer, which is then bolted to the main extruder body with long bolts.
ReplyDeleteTwo important issues:
1) The PTFE thermal barrier will get soft at the 220C temps needed by the extruder for ABS. This, with the pressure of the filament being forced in from above, will usually eventually push the brass barrel out the bottom, stripping the PTFE threads, and ruining the thermal barrier. To solve this, get a low profile 6mm jam nut and screw it onto the brass barrel. Now, put the brass barrel fully onto the PTFE barrier, and then snug the nut up against the PTFE barrier. The nut should now be between the PTFE barrier and the retainer washer. This transfers the force from the barrel to the retainer washer directly, and relieves the pressure on the PTFE threads.
2) Having done the above, the PTFE barrier may still be soft enough to bulge out to the sides, letting the extrudant squeeze into the space between the brass barrel and the PTFE threads. This increases the force needed to push the filament through the barrel, and eventually stops extrusion. To fix this, get a 1/2" pipe/hose clamp and tighten it down halfway up the PTFE barrier, right where the brass barrel should end inside.
I went through five PTFE barriers before I did these two mods.
I was also thinking of getting one of those newer hybrid PTFE/PEEK barriers that refsnyderb is selling, seems to have the best of both worlds. When i was doing my recent heating tests on the converted MakerBot, the PTFE did get really hot, so I might try and rig something up to help captivate the barrel, most likely similar to the plastruder setup.
ReplyDelete